The Importance of Fuel Lubricity in Diesel Engines: Ensuring Longevity and Performance
- Folio Instruments
- Oct 22, 2024
- 9 min read
In diesel engines, the quality of fuel extends beyond power and efficiency; it is vital for maintaining the longevity of engine components. One key factor in this is fuel lubricity: the ability of the fuel to reduce friction and prevent wear on critical parts such as fuel injectors and pumps. Adequate lubricity is essential to prevent excessive wear. The transition to ultra-low-sulphur diesel (ULSD), driven by stringent environmental regulations, has made maintaining sufficient lubricity more challenging. Historically, sulphur in diesel fuel provided natural lubrication, but as sulphur content has decreased, so has the lubricity of these fuels. This shift underscores the need for effective solutions to enhance and measure lubricity in low-sulphur diesel.
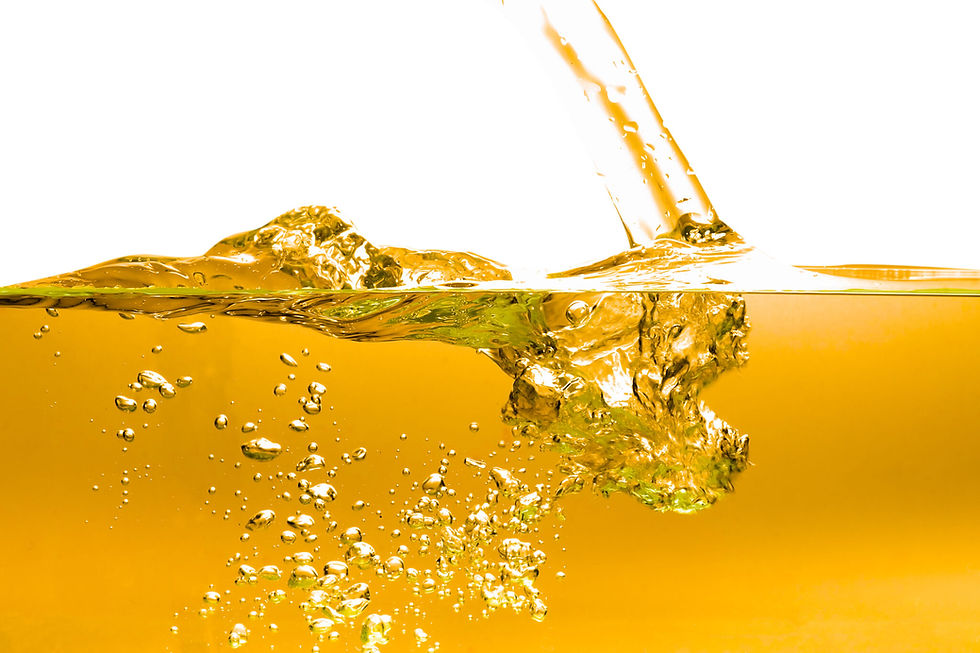
In this article, we explore the scientific principles behind fuel lubricity, examining how it influences engine performance and component durability. In this article, we will review the testing methods used to evaluate fuel lubricity, including the High-Frequency Reciprocating Rig (HFRR) and industry standards such as ISO 12156 and ASTM D6079. Additionally, we will discuss the role of additives in improving fuel performance and restoring lubricity in ULSD. By examining these aspects, we aim to provide a comprehensive understanding of how to address lubricity challenges and ensure engine protection and efficiency.
Understanding Fuel Lubricity and Its Role in Diesel Engines
Fuel lubricity refers to the fuel’s ability to prevent wear and tear on the engine components it contacts, such as fuel injectors and pumps. These components are integral to the operation of a diesel engine, ensuring the precise delivery of fuel into the combustion chambers. When these parts are not adequately lubricated, they can wear out prematurely, leading to increased maintenance costs, reduced engine performance, and ultimately, a shorter engine life.
Historically, diesel fuels contained high levels of sulphur, which provided necessary lubrication for these critical components. The presence of sulphur acted as a natural lubricant, helping to reduce friction and wear. However, the drive to reduce sulphur content in diesel fuel for environmental reasons has introduced significant challenges: low-sulphur diesel fuels lack the natural lubricity of their predecessors, leaving engine components more vulnerable to wear and tear. Studies have shown that this reduction in sulphur content correlates with increased wear rates in fuel injectors and pumps due to inadequate lubrication [1].
The Mechanical Implications of Reduced Lubricity
The mechanical implications of reduced lubricity are significant. Without the natural lubricating properties provided by sulphur, diesel engine components are more susceptible to issues such as shearing and micropitting. Shearing refers to the breakdown of lubricating films, which increases friction and wear, while micropitting involves the formation of small pits or indentations on metal surfaces due to repeated stress and inadequate lubrication [2]. Both phenomena can accelerate the degradation of engine parts and negatively impact overall performance.
To address these lubricity challenges posed by low-sulphur diesel, various additives have been explored. Research indicates that fatty acid methyl esters, derived from biofuels, can serve as effective lubricating additives. For instance, Liu et al. (2019) demonstrated that adding fatty acid methyl esters to ultralow-sulphur diesel fuel significantly improved its lubricating properties, reducing wear and friction in engine components [3]. These additives work by forming a protective layer on metal surfaces, similar to the function of sulphur in traditional diesel fuels. The introduction of these additives underscores the necessity for standardised testing to ensure that diesel fuels meet minimum lubricity requirements. The High-Frequency Reciprocating Rig (HFRR) is one such tool used to evaluate and maintain fuel lubricity standards, providing a reliable measure of the lubricating properties of diesel fuels. The HFRR test is critical in assessing how different formulations, including biodiesel blends, affect fuel lubricity and engine performance [2].
The Shift to Low-Sulphur Diesel and Its Consequences
In response to growing environmental concerns, regulations were implemented to drastically reduce the sulphur content in diesel fuels. This led to the widespread adoption of ultra-low-sulphur diesel (ULSD), which contains significantly less sulphur than traditional diesel fuels. While ULSD has been effective in reducing harmful emissions such as sulphur oxides (SOX), it has introduced a new set of challenges related to fuel lubricity.
Impact on Fuel Lubricity
Sulphur in diesel fuel historically provided essential lubricating properties that protected critical engine components. The reduction in sulphur content with the advent of ULSD resulted in a significant decrease in the natural lubricity of diesel fuels. This change had immediate consequences for the diesel engine industry. Reports emerged of increased wear and tear on fuel system components, including more frequent fuel pump failures and injector malfunctions [1]. The decrease in lubricity led to higher friction between moving parts, accelerating the wear and potentially shortening the lifespan of these components [2].

In order to illustrate the urgency of addressing lubricity challenges, consider a scenario where a fleet of delivery trucks experiences unexpected downtime due to fuel pump failures. This situation has become increasingly common for operators facing mounting repair costs, highlighting the critical need for effective lubricity solutions to maintain efficient operations.
Industry Response and Additives
To mitigate the negative effects of reduced lubricity, the industry sought solutions in the form of lubricity additives. These additives were designed to replicate the lubricating properties that sulphur once provided. Research into various additives, including biodiesel and synthetic lubricants, demonstrated their effectiveness in enhancing the lubricity of ULSD. For instance, studies have shown that biodiesel blends can significantly improve the lubricating characteristics of ULSD fuels [3]. These additives help form a protective layer on metal surfaces, reducing friction and wear.
Need for Reliable Testing Methods
The introduction of lubricity additives underscored the necessity for reliable testing methods to ensure that diesel fuels meet the required lubricity standards. The High-Frequency Reciprocating Rig (HFRR) has become a crucial tool in this regard. It allows for the consistent measurement of fuel lubricity, ensuring that all diesel fuels, regardless of their sulphur content or additives, provide adequate protection for engine components. By adhering to established standards such as ISO 12156, ASTM D6079, and ASTM D7688, the industry can better manage the trade-offs between environmental benefits and engine performance [1].
Comparison with Other Fuels
Understanding the challenges of fuel lubricity in diesel engines becomes clearer when compared to other types of fuels. Diesel fuels, particularly ultra-low-sulphur diesel (ULSD), face unique lubrication challenges due to historical reliance on sulphur for natural lubrication. In contrast, other fuels like gasoline and alternative options such as biodiesel and ethanol have different properties and requirements. This comparison helps illuminate why diesel fuels require specific solutions for maintaining lubricity and highlights how alternative fuels address or sidestep these challenges in various ways.
Diesel vs. Gasoline
Lubricity Requirements: Diesel engines generally require higher lubricity fuels than gasoline engines due to the high pressures and temperatures within the diesel fuel system. Gasoline engines, by contrast, often rely on different lubrication strategies within their systems, and the lubricity of gasoline is less critical compared to diesel.
Fuel Composition:Unlike diesel fuels, which historically relied on sulphur for lubrication, gasoline has different chemical properties and does not face the same issues with reduced natural lubricity. This is partly because gasoline engines typically operate at lower pressures and temperatures.

Alternative Fuels
Biodiesel: Biodiesel is often used to enhance the lubricity of ultra-low-sulphur diesel (ULSD). It can provide natural lubricating properties similar to those lost when sulphur was removed from diesel fuels. Research has shown that biodiesel blends can effectively restore lubricity and improve engine performance [1][3].
Ethanol: Ethanol, commonly used in gasoline blends, does not significantly impact lubricity in the same way as biodiesel. However, ethanol can influence fuel system components due to its different chemical characteristics and can potentially affect engine performance if not properly managed.
Hydrogen: Hydrogen is a promising alternative fuel with no lubricating properties because it is not a liquid fuel. Its use in fuel cells involves different technology and doesn’t directly affect lubricity in the traditional sense. However, its introduction into the fuel market will require new strategies for engine design and fuel system management.
The Development of Fuel Lubricity Standards and Testing
The rapid changes in fuel composition and the resulting challenges underscored the necessity of standardised testing to ensure that all diesel fuels met a minimum level of lubricity. This is where the High-Frequency Reciprocating Rig (HFRR) came into play. The HFRR is an essential tool in the development and enforcement of fuel lubricity standards worldwide.
PCS Instruments’ HFRR is at the forefront of this effort, playing a critical role in establishing and maintaining key international standards such as ISO 12156, ASTM D6079, and ASTM D7688. These standards ensure that diesel fuels provide sufficient lubrication to protect engine components, regardless of the sulphur content. By adhering to these standards, fuel producers can guarantee that their products will not contribute to the premature wear of diesel engines, thereby safeguarding the longevity and reliability of these machines.
Following the introduction of the HFRR, it’s worth noting research that further validates the effectiveness of this testing method. A study comparing the lubricant characteristics of various paraffinic diesel fuel formulations-including biodiesel blends and fuels with lubricity improvers-demonstrated that the HFRR test is more restrictive and severe than the SL-BOCLE test. Notably, the study found that no paraffinic diesel sample that performed well in the HFRR test performed poorly in the SL-BOCLE test, confirming the HFRR’s reliability. This research underscores that the HFRR test alone is sufficient to certify the lubricity of diesel fuels, eliminating the need for additional tests like SL-BOCLE. This reinforces the critical role of the HFRR in ensuring that modern diesel fuels meet the necessary lubricity standards to protect engine components [1].
The Role of ZDDP in Combating Wear and Environmental Impacts
As diesel fuel lubricity decreases with the reduction of sulphur, engine components become more prone to wear and scarring, especially between metal parts that rely on fuel lubrication. ZDDP (Zinc Dialkyl Dithiophosphate), an anti-wear additive found in engine oils, has long been recognised for its ability to protect metal surfaces by forming a protective film that reduces friction. Shearing and Micropitting are two specific wear phenomena that can occur when lubricity is insufficient:
Shearing refers to the deformation of metal surfaces when the lubricating film between them breaks down. The reduced lubricity in fuels like ULSD can lead to increased metal-on-metal contact, intensifying friction and accelerating wear.
Micropitting is a form of surface fatigue that results in small craters or pits forming on metal surfaces due to cyclic loading. This form of damage weakens the integrity of components and can lead to premature failure. Insufficient lubrication exacerbates micropitting, causing long-term degradation.
ZDDP plays a crucial role in preventing both shearing and micropitting by enhancing the protective film on engine parts. However, balancing the benefits of ZDDP with environmental regulations remains a challenge, as ZDDP can harm catalytic converters and increase emissions.
Environmental Considerations
While ZDDP is effective in combating wear, it has drawn scrutiny due to its environmental impact, particularly its effect on emissions control systems. Modern regulations have limited the amount of ZDDP that can be used in engine oils, making it crucial to find alternatives or improve additive formulations that meet both environmental and performance standards. Fuel additives, such as biodiesel, are increasingly seen as eco-friendly solutions to the lubricity issue. Studies have shown that biodiesel blends can improve the lubricity of ULSD without the negative environmental side effects of ZDDP. These bio-additives provide a renewable, lower-emission alternative that enhances lubricity and reduces wear in diesel engines [1][2][3].
The Critical Role of Lubricity in Modern Diesel Engines
As diesel technology advances, the critical importance of maintaining fuel lubricity is increasingly evident. Modern diesel engines, engineered with tighter tolerances, are more sensitive to fuel quality than ever before, making adequate lubricity essential for optimal performance and longevity. The transition to ultra-low-sulphur diesel (ULSD) has transformed the lubricating landscape; the removal of sulphur—historically a natural lubricant—has led to heightened wear on key components. Reports of increased failures in fuel pumps and injectors highlight the urgent need for effective lubrication solutions, with studies indicating that the reduction in sulphur correlates with increased wear rates in these critical parts [1][2].
In response to these challenges, the industry is actively investigating innovative additives, particularly those derived from biodiesel. Research has shown that fatty acid methyl esters can enhance the lubricity of ULSD by forming protective films on metal surfaces, potentially reducing wear [3]. While biodiesel blends show promise in improving lubricity, variability in biofuel quality and production scalability underscores the need for further study and standardisation to ensure consistent performance across formulations.
To support these advancements, rigorous testing standards are more critical than ever. The High-Frequency Reciprocating Rig (HFRR) plays a pivotal role in this landscape, providing reliable measurements of lubricity that enable fuel producers to refine formulations to meet both performance and regulatory demands. The HFRR has been instrumental in establishing key international standards for lubricity testing, ensuring that diesel fuels provide adequate protection for engine components [1].

Looking ahead, the focus on lubricity will remain vital as the diesel industry evolves. Continued research into new additives and formulations will be essential to navigate the dual challenges of environmental regulations and engine protection. With organisations like PCS Instruments at the forefront of testing and standardisation, the future of diesel engines promises to integrate innovation and sustainability while maintaining high performance.
Final Takeaways
As we navigate the complexities of modern diesel technology, the critical importance of fuel lubricity becomes increasingly clear. The transition to ultra-low-sulphur diesel (ULSD) has presented significant challenges, but it has also sparked innovation within the industry. By continuing to explore effective additives and biofuels, we can restore lubricity and ensure the longevity of diesel engines. Rigorous testing and adherence to established standards, such as those maintained by PCS Instruments, will be essential in this pursuit.
Looking ahead, the future of diesel technology holds promise. With ongoing research and collaboration, we can develop solutions that balance performance with environmental sustainability. As the industry adapts to new regulations and consumer expectations, a commitment to enhancing fuel lubricity will not only support the durability of diesel engines but also contribute to a more sustainable automotive landscape.
References
Barbour, R. H., Rickeard, D. J., & Elliott, N. G. (2000). Understanding Diesel Lubricity. SAE Transactions, 109, 1556–1566. http://www.jstor.org/stable/44745957
Energy Fuels. (2020). The lubricant characteristics of different paraffinic diesel fuel formulations. Energy & Fuels, 34(3), 2654–2664. https://doi.org/10.1021/acs.energyfuels.9b03169
Liu, X., Wang, L., & Li, M. (2019). Evaluation of fatty acid methyl esters as lubricating additives in ultralow-sulfur diesel fuel. Fuel, 235, 1327-1335. https://doi.org/10.1016/j.fuel.2018.08.009
Comments